Kanban is a workflow management method that helps teams visualize work, maximize efficiency, and improve continuously. Originating from manufacturing, kanban has now been adopted by agile software teams and business units across industries to optimize processes. This article provides an in-depth look at what kanban is, how it works through kanban boards, core practices, and key benefits for teams.
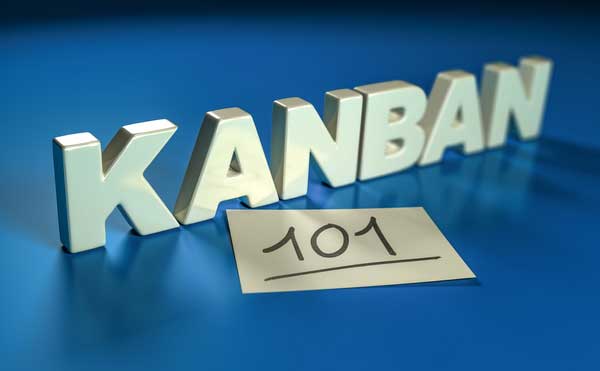
What is Kanban?
Kanban is a Japanese word that means “signboard” or “billboard.” As a workflow management system, kanban involves visually mapping out a team’s work process using boards, cards, and work-in-progress limits to highlight bottlenecks, gaps, and opportunities for improvement.
The kanban method originated on the factory floors of Toyota in the late 1940s. Toyota began optimizing its just-in-time manufacturing process based on the same model that supermarkets were using to stock their shelves. By decreasing excess inventory and aligning materials to consumption, Toyota gained efficiency.
On the factory floor, workers would pass a card or “kanban” between teams when materials were used up. This allowed everyone to communicate capacity levels and ensure the next batch of needed materials was ready to go. As technology evolved, so did kanban, but the transparency of the process has remained essential.
What is a Kanban Board?
A kanban board visually maps out the workflow process in vertical lanes marked “to do,” “doing,” and “done.” More complex workflows can have sub-lanes with additional steps defined.
For example:
- To Do
- To Do – Unprioritized
- To Do – Prioritized
- Doing
- Plan
- Develop
- Test
- Launch
- Done
- Done – Pending Approval
- Done – Completed
Team members can see the status of every work item at any time, ensuring full traceability and enabling faster problem identification.
Kanban Cards
Kanban cards represent individual work items and provide critical details about each task. This allows the team visibility into who is responsible for what piece of work, an estimated timeframe, technical specifications, and more.
Kanban cards give transparency into work progress and details so that nothing gets missed or delayed unnecessarily. Team members can also easily identify dependencies and bottlenecks when everything is visually mapped.
Core Practices of the Kanban Method
While implementing kanban, teams should focus on these essential practices:
- Visualize Workflow
- The kanban board should show each step of the process work items go through, work-in-progress limits, and policies guiding what work exists in each stage.
- Limit Work In Progress
- By limiting the amount of work happening at once, teams complete existing items first before taking on new work. This smooths flow, reduces bottlenecks, and improves focus.
- Manage Flow
- Kanban highlights workflow stages and status so teams can analyze processes to reduce lead times, maximize value, and balance speed with quality. Addressing bottlenecks is key.
- Make Policies Explicit
- If processes aren’t clearly defined and understood by all team members, they can’t be improved. Visible, published policies aligned to goals boost collaboration.
- Implement Feedback Loops
- Getting regular customer feedback, especially early on, ensures the end product meets expectations in the shortest time possible.
- Improve Continuously
- Teams must collaboratively implement changes using metrics and empirical data to drive continuous improvement framed as hypothesis testing.
Benefits of Using Kanban
Adopting the kanban workflow method offers many advantages, including:
- Identifying Issues
- Work-in-progress limits highlight barriers so teams can address lack of focus, resources, or techniques.
- Flexibility
- Kanban isn’t restrictive – there are no fixed durations and priorities shift based on the latest data, making it widely adaptable.
- Saving Time
- The visual process improves collaboration and surface issues early so they can be fixed quickly, saving time.
- Empowering Teams
- Access and shared responsibility foster better communication and skills.
- Balancing Productivity
- Limiting work-in-progress prevents workers getting bogged down in one task.
- Increasing Customer Satisfaction
- Fine-tuned results that meet client expectations are driven through work-in-progress limits.
In today’s complex business environment, implementing efficient workflow systems offers teams huge advantages. Originating from lean manufacturing, the kanban process leverages key techniques like visualization, work-in-progress limits, and continuous improvement to drive better outcomes. Any knowledge work team struggling with bottlenecks, overburdening, or lack of transparency can benefit greatly from adopting kanban practices.
Conclusion
From software development to marketing to HR, kanban has become an essential way for teams across departments and industries to optimize their systems. By visualizing workflow, limiting work-in-progress, implementing feedback loops and driving continuous incremental improvement, the kanban method helps teams boost performance, quality, speed to market and more. Its flexibility and focus on empiricism over rigid rules ensure it can be molded to fit any team’s needs.
Whether just starting to experiment with process improvements or needing to better align across complex multi-team efforts, implementing kanban boards, work-in-progress limits, and other practices will quickly illuminate gaps and opportunities for positive change. As kanban founder David Anderson wrote, “With kanban, every process should be challenged to be explicitly understood, agreed to, and improved.”