Lean manufacturing is a production process that focuses on maximizing productivity while minimizing waste. Many manufacturers are using lean principles to eliminate waste, optimize processes, reduce costs, boost innovation and speed time-to-market.
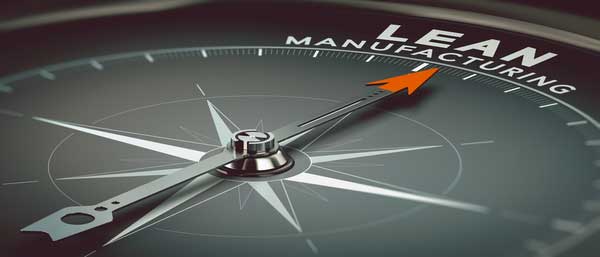
What is Lean Manufacturing?
Lean manufacturing is a production philosophy that aims to deliver maximum value to the customer while reducing waste. The main goal is to optimize workflows and processes to sustainably deliver value to the customer.
Although eliminating waste is a key part of lean, the ultimate objective is to provide the maximum value to the customer. Well-known companies using lean manufacturing include Toyota, Intel, John Deere and Nike.
5 Core Principles of Lean Manufacturing
The book “Lean Thinking” outlined five core principles that serve as the foundation for lean methodology:
Value
Value is defined from the customer’s perspective. It refers to what they are willing to pay for a product or service. Manufacturers should focus on delivering optimal value to the customer while maximizing profits.
Map the Value Stream
Analyze all the steps and resources needed to provide a product or service. Identify and eliminate any waste to optimize the value stream.
Create Flow
Eliminate barriers and bottlenecks to ensure smooth flow of processes with minimal delays or waste. Lean relies on integrated, streamlined processes.
Establish Pull System
Only produce or acquire inventory based on actual customer demand instead of forecasts. This minimizes excess inventory and related costs.
Pursue Perfection
Continuously improve processes through small changes to target root causes of defects and eliminate waste. Also known as Kaizen.
8 Forms of Waste in Lean
The acronym DOWNTIME summarizes the 8 categories of waste targeted in lean manufacturing:
- Defects – Errors, mistakes, poor quality
- Overproduction – Producing more or faster than needed
- Waiting – Idle time waiting for people, parts, equipment
- Non-utilized Talent – Underutilizing skills and experience
- Transportation – Unnecessary movement of materials or products
- Inventory – Excess stock and inventory
- Motion – Unnecessary movement by employees
- Excess Processing – Extra steps that don’t add value
Benefits of Implementing Lean Manufacturing
Some key benefits of lean manufacturing include:
Increased Efficiency
More efficient workflows, resource use and production can benefit any business. This allows for reduced lead times and better customer service.
Cost Savings
Eliminating waste directly translates into lower costs. Lean enables businesses to operate with fewer resources.
Environmental Sustainability
Removing excess processes reduces energy and fuel usage. Energy efficient equipment also provides environmental and cost benefits.
Improved Customer Satisfaction
Delivering the right product or service, at the right time and price increases customer satisfaction. This drives loyalty and business growth.
Potential Drawbacks of Lean Manufacturing
However, there are some potential downsides to keep in mind:
Employee Safety Risks
Pushing for maximum efficiency can sometimes override safety. Care must be taken to avoid employee burnout or injuries.
Lack of Long-Term Focus
An obsessive focus on cutting waste can distract from long-term innovation and growth. A balance is needed between short-term efficiency and long-term development.
Conclusion
Lean manufacturing can help companies maximize productivity, reduce costs and provide greater value to the customer when implemented properly. However, the principles of lean should be adapted carefully to suit each organization’s specific needs and challenges. Sustained commitment from leadership and engagement of employees at all levels is key to realizing the full benefits of lean.