In today’s competitive business landscape, organizations strive to deliver consistent quality products and services to meet customer expectations. One effective way to achieve this is by implementing the ISO 9001 Quality Management System. Whether it’s the ISO 9001, ISO 14001, ISO 45001, or ISO 27001, these standards share a common framework that can work wonders for your organization. In this article, we will delve into the details of the ISO 9001 Quality Management System, exploring its components and how it can benefit your business.
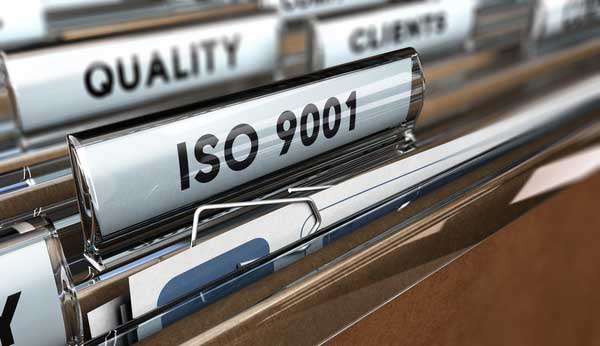
Understanding the ISO 9001 Framework
The ISO 9001 Quality Management System is built upon a framework that consists of 10 clauses. These clauses form the foundation of the system and guide organizations in their pursuit of quality excellence. The clauses include:
- Scope
- Normative Reference
- Terms and Definitions
- Context of the Organization
- Leadership
- Planning
- Support
- Operation
- Performance Evaluation
- Improvement
It’s important to note that clauses 1, 2, and 3 are not explicitly mentioned in the model. The requirements are contained from clause 4 up to clause 10, which are the nuts and bolts of the Quality Management System. Each of these clauses is critical, and removing any one of them can result in the breakdown of the system.
The Customer-Centric Approach
At the heart of the ISO 9001 Quality Management System lies a customer-centric approach. The left side of the model represents customer requirements, while the right side represents customer satisfaction. Bridging the gap between these two is crucial for organizational success. To do so, a robust and reliable Quality Management System must be established at the center of the canvas.
The left side of the model emphasizes understanding customer requirements and the context of the organization. By grasping these elements, organizations can develop a plan to meet customer expectations and achieve customer satisfaction, which are represented on the right side of the model. This customer-focused approach ensures that organizations consistently produce quality results.
Establishing a Robust Quality Management System
To ensure consistent and quality results, organizations need to establish a strong Quality Management System. Clause 4 of ISO 9001 emphasizes defining the context of the organization and capturing customer requirements, including the needs and expectations of relevant interested parties. This step serves as the starting point for every business.
Leadership plays a significant role in this new addition of ISO 9001. Unlike the previous version, where leadership was delegated to the Quality Management Representative, the new ISO 9001 places importance on the commitment and involvement of leaders at all levels of the organization. Effective communication of the importance of meeting client expectations and a customer-focused mindset are key aspects of leadership.
Planning for Success
Clause 6 of ISO 9001 guides organizations in planning their actions to address risks and opportunities. This proactive approach allows organizations to identify potential pitfalls and capitalize on opportunities. Defining quality objectives and developing a clear plan to achieve them is vital. It’s crucial to monitor and make necessary changes to these objectives and actions as required.
Critical Support for Success
No organization can thrive without adequate support. ISO 9001 defines critical support areas that organizations must focus on:
- Resources: This includes competent and motivated personnel, adequate infrastructure, and a favorable work environment that facilitates efficient process operations. Monitoring and measuring the use of resources is also important.
- Competence: Ensuring that employees possess the necessary skills and knowledge to perform their tasks effectively is crucial. Training and development programs play a vital role in building competence.
- Awareness: Raising awareness about quality management principles, processes, and objectives among employees fosters a culture of quality throughout the organization.
- Communication: Effective communication channels must be established to facilitate the flow of information regarding quality management system requirements and expectations.
- Documented Information: Documented information, such as quality manuals, procedures, work instructions, forms, and records, provides a reference for employees and ensures consistency in processes.
Operational Excellence
The operation phase of the ISO 9001 Quality Management System is where things get done. It involves the production of products or the delivery of services. This stage is often challenging, as it requires organizations to maintain strict control over their processes. The quality of the results depends on the quality of the controls established in this phase.
Clause 8 of ISO 9001 guides organizations on how to plan and control operations. This includes accurately capturing customer requirements, designing and developing products and services, controlling outsourced processes, and managing post-delivery activities. By adhering to these guidelines, organizations can ensure that their operations meet customer expectations consistently.
Performance Evaluation and Continual Improvement
At the end of the day, organizations need to assess whether they have met customer expectations and requirements. Clause 9 of ISO 9001 emphasizes the importance of performance evaluation through monitoring, measurement, analysis, and evaluation using key performance indicators (KPIs). Regular internal audits provide valuable data for management to review and identify areas that need improvement or change.
W. Edwards Deming, a renowned quality guru, famously said, “Without data, you’re just another person with an opinion.” The effectiveness of performance evaluation depends on the accuracy of data and its analysis. Acting upon the findings completes the Plan-Do-Check-Act (PDCA) cycle, paving the way for continual improvement.
Conclusion
The ISO 9001 Quality Management System provides organizations with a framework to achieve consistency and quality in their products or services. By understanding the various clauses and implementing a robust Quality Management System, organizations can bridge the gap between customer requirements and customer satisfaction. Key elements such as leadership, planning, support, and performance evaluation play crucial roles in this journey. Completing the PDCA cycle and obtaining ISO 9001 certification can instill confidence in customers, enhance organizational efficiency, and drive continual improvement. Embrace the ISO 9001 Quality Management System, and unlock the path to excellence.