In the fast-paced world of project management, delivering top-notch results is paramount. However, success hinges on more than just completing tasks on time and within budget. It’s about ensuring that every aspect of the project meets or exceeds customer expectations – and that’s where quality management comes into play. This comprehensive guide delves into the intricacies of quality management in project management, exploring its significance, principles, and practical implementation.
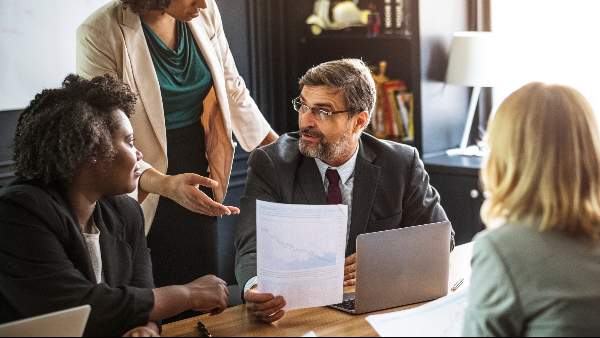
Understanding Quality Management in Project Management
Quality management is the backbone of successful project delivery. It’s a systematic approach that encompasses a set of processes, policies, and procedures designed to ensure that projects consistently meet or exceed customer requirements. Just as a well-crafted recipe guarantees delectable cookies, quality management serves as a recipe for project success, guiding every step from inception to completion.
At its core, quality management revolves around three fundamental elements: quality planning, quality control, and quality assurance. Together, these components work in harmony to establish clear quality objectives, monitor and verify compliance, and prevent defects or deviations from defined standards.
The Importance of Customer Requirements
The starting point of any quality management endeavor is a deep understanding of customer requirements. These requirements encompass the expectations, needs, and specifications that customers have regarding the products or services being delivered. By placing customers at the center of every decision and process, organizations can ensure that their projects consistently deliver value and exceed expectations.
Quality planning plays a crucial role in translating customer requirements into actionable objectives and standards. It involves defining clear quality goals, identifying the resources required to achieve them, and establishing the processes and procedures that will guide the project towards success.
Quality Control: The Vigilant Guardian
Quality control is the watchful eye that ensures projects adhere to defined standards throughout the production process. It involves a range of activities, including inspections, tests, and measurements, designed to catch any defects or deviations from the norm. Like a vigilant guardian, quality control catches mistakes before they escalate, minimizing the risk of delivering subpar products or services.
However, quality control goes beyond merely identifying issues; it also involves implementing corrective actions to address any identified problems. This proactive approach ensures that projects stay on track and maintain the highest levels of quality.
Quality Assurance: Preventing Mistakes Before They Happen
While quality control focuses on catching mistakes, quality assurance takes a proactive approach to preventing them from occurring in the first place. It involves establishing robust systems and procedures that embed quality into every step of the project lifecycle, from design to delivery.
Quality assurance encompasses a wide range of activities, such as process audits, supplier evaluations, and training programs. By identifying and addressing potential issues before they manifest, quality assurance helps organizations maintain a consistently high level of quality, reducing the need for costly rework or corrections.
Continuous Improvement: The Secret Ingredient
In the dynamic world of project management, standing still is not an option. Continuous improvement is the secret ingredient that keeps quality management systems thriving and organizations ahead of the curve. It’s a never-ending cycle of gathering feedback, analyzing data, and implementing iterative enhancements to processes, products, and services.
Continuous improvement encourages organizations to embrace change, learn from experience, and adapt to evolving customer needs and market trends. By fostering a culture of continuous learning and improvement, organizations can consistently exceed customer expectations and maintain a competitive edge.
Principles of an Effective Quality Management System
Establishing an effective quality management system (QMS) requires adhering to a set of guiding principles that promote quality-focused decision-making and organizational excellence. These principles include:
- Customer Focus: Placing the customer at the center of all processes and decisions, ensuring that products and services consistently deliver value and exceed expectations.
- Leadership: Effective leadership that establishes a clear vision, sets quality objectives, and fosters a supportive environment where employees are motivated to contribute to the QMS.
- Involvement of People: Recognizing that employees are the driving force behind quality, a QMS encourages the involvement and empowerment of people at all levels, leveraging their skills, knowledge, and expertise.
- Process Approach: Adopting a process-oriented approach, viewing activities as interconnected processes that collectively contribute to achieving quality objectives.
- Systematic Approach to Management: Emphasizing the importance of a systematic approach to managing quality, identifying, analyzing, and managing interrelated processes to ensure consistency, reliability, and effectiveness.
- Continual Improvement: Embracing a mindset of continuous improvement, actively seeking opportunities for enhancement, gathering data and feedback, and implementing changes to enhance products, processes, and systems.
- Factual Decision-Making: Basing decisions on factual analysis and data-driven insights rather than assumptions or personal opinions, ensuring that choices are informed and lead to better outcomes.
- Mutually Beneficial Supplier Relationships: Recognizing the importance of strong, collaborative relationships with suppliers, based on shared goals and trust, to ensure the quality of incoming materials, enhance supply chain efficiency, and deliver value to customers.
By embracing these principles, organizations can establish a robust QMS that drives continuous improvement, customer satisfaction, and sustainable success.
Conclusion:
Quality management is an indispensable component of successful project management. It provides a structured approach to ensuring that projects consistently meet or exceed customer expectations, from quality planning and control to assurance and continuous improvement. By adopting a customer-centric mindset, implementing robust quality processes, and fostering a culture of continuous learning and enhancement, organizations can achieve project excellence, build long-lasting customer relationships, and maintain a competitive edge in today’s ever-evolving business landscape